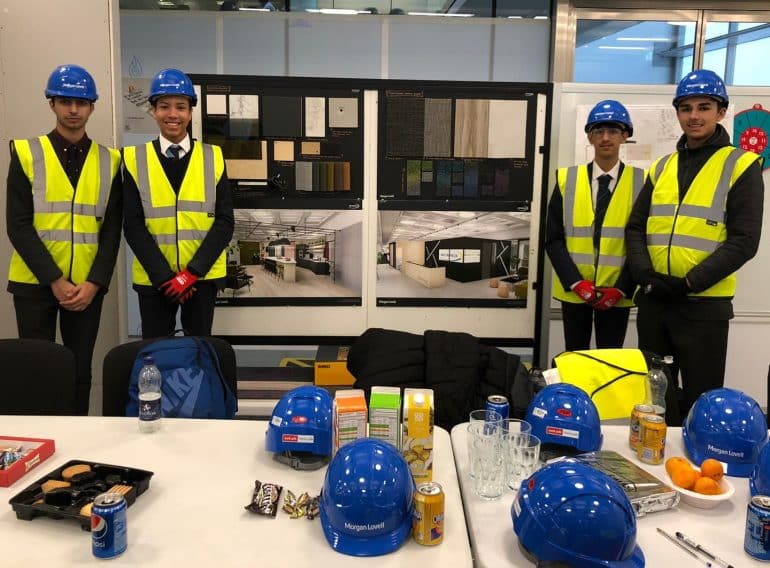
A Sixth Form engineering team’s innovative design project aimed at reducing the risk of injury from band saws is in the running for a major construction industry award.
The Year 12 team’s suggested improvements to band saw guards and dust extraction systems have been nominated for an Innovation Award in the annual Constructing Excellence SECBE Awards 2020 finals, where their fellow competitors include professional firms working in the industry. They are also hoping to win a new award introduced this year – the People’s Choice award, which is decided by popular vote.
The four boys – Brandon Ionev, Thomas Mgbor, Kai Sethna and Hugh Westcott – worked with office design specialists Morgan Lovell on the project. With the nomination, the four are following in the footsteps of other QE EES teams of recent years whose inventions under the Engineering Project Challenges initiative have achieved regional and national success.
Their entry was one of just two in their category to be selected by the judges to be interviewed in a ‘head-to-head’ at the virtual awards ceremony on Thursday 2nd July.
QE’s Head of Technology, Michael Noonan, said: “My congratulations go to these four students, who worked hard to come up with innovative designs that fulfilled the brief and were based on sound engineering principles. With the support of the Elizabethan community, they also stand a good chance of clinching the People’s Choice Award. We think they thoroughly deserve it, so please cast your vote now! Thank you.”
The deadline for voting is 5pm on Thursday 2nd July. To vote, visit the awards page describing the boys’ entry, scroll to the bottom and click the People’s Choice button.
During visits to construction sites, boys saw that workers often fail to use the blade guard fitted to existing band saws, because it is tedious and time-consuming to reset the guard manually each time to adjust it for different thicknesses of material.
To address the issue, the boys conducted extensive research over six months. They came up with three designs, all with the same basic idea. The material pushes against the bottom of the blade guard, causing a force that pushes upwards and adjusts the blade guard automatically to the correct and ideal height for cutting. Two of the designs use simple rails and sliders to autonomously adjust the height, while the third uses a rack and pinion. With no user input needed, saw operators can work in the same way as before, but much more safely.
An additional benefit of the designs is that they incorporate significant improvements to the existing dust extraction systems of saws, thus reducing dust exposure – another health & safety concern – and allowing a more precise cut to be made because of the enhanced visibility of the cutting service.
The designs would work with different types of saw and, unlike existing guards, they cover the blade from multiple angles, which is another safety improvement. Because they can be retrofitted to existing machines, the guards hold out the promise of improving safety without huge expenditure. The boys were assisted by their industry mentor, representing Morgan Lovell, Health Safety & Wellbeing Manager Alex Wood.
During the spring, just before the COVID-19 social distancing measures were put in place, the Morgan Lovell team and a second QE team working with Morgan Lovell’s sister company, Overbury, gave presentations on their projects to members of the Institution of Occupational Safety and Health (IOSH, a UK-based global chartered body for health & safety professionals), at UBM’s centre, close to Blackfriars Bridge in London.